.jpg)
In our project the Flow Focusing technique is used to generate micrometer-scale sphere particles with mono disperse size distribution. In our project Flow Focusing technique utilizes the focusing of a disperse phase (a stream of polymer dissolved in chloroform) by a continues phase(water) liquid driven by a pressure drop. In this technique the continues phase fluid exerts pressure and viscous stress that force the dispersed phase fluid into a microthread. The breakup of the microthread then takes place inside of downstream of the orifice. The droplet breakup is a sensitive process and require skilful control of the fluid flow in the channels. Monodisperse droplets with a wide range of average diameter can be generated using this technique. Interestingly, the use of flow focusing technique which formed the microthread of the dispersed phase, is also allow generation of monodispersed droplets with diameter much smaller then the orifice size.
It is observed that the width of microthread at the channel junction decreased with increasing flow rates of the dispersed phase and the continues phase. When the microthread attained a characteristic width of several micrometers, droplet breakup occurred near the channel junction, which is independent of the flow rate of the dispersed phase.
Flow Focusing ray diagram:
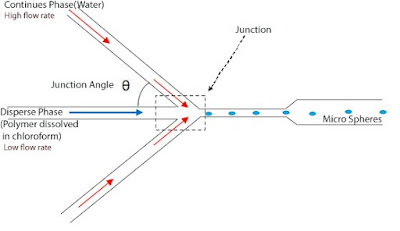
Effect of Junction Angle on the size of microspheres:
The effect of junction angle θ, in flow-focusing geometry on droplet formation is described here. Consider six microfluidic channel patterns with varied geometries. The schematic of the microfluidic channel pattern is shown in Figure. Each microfluidic Flow-Focusing device is comprised of three inlets with a common flow- focusing area. Inject the continues phase (stream of water) into two side inlet channels and a stream of polymer dissolved in chloroform as disperse phase into the middle inject channel. No surfactant should be added to either phase.

In the experiment[Reference], the flow rate of disperse phase is fix at Qo, while varying the continues phase flow rate Qw. Five different continues flow rates Qw (50μl/h ≤ Qw ≤ 250μl/h) and two different disperse phase flow rates Qo (Qo =10μl/h, 20μl/h) are chosen. The complete process is observed under an inverted optical microscope. The sizes of droplets are measured by photographs taken by a CCD camera; coupled to the microscope. Researches usually uses image analysis software (Imaging Pro Plus 5.1, Media cybernetics, Inc.) to measure the sizes of the droplets and calculate the size distributions with coefficients of variation (CV) in diameter.
***************************************************************************************************************************************************************************************